quality accelerated
by IT facilitation
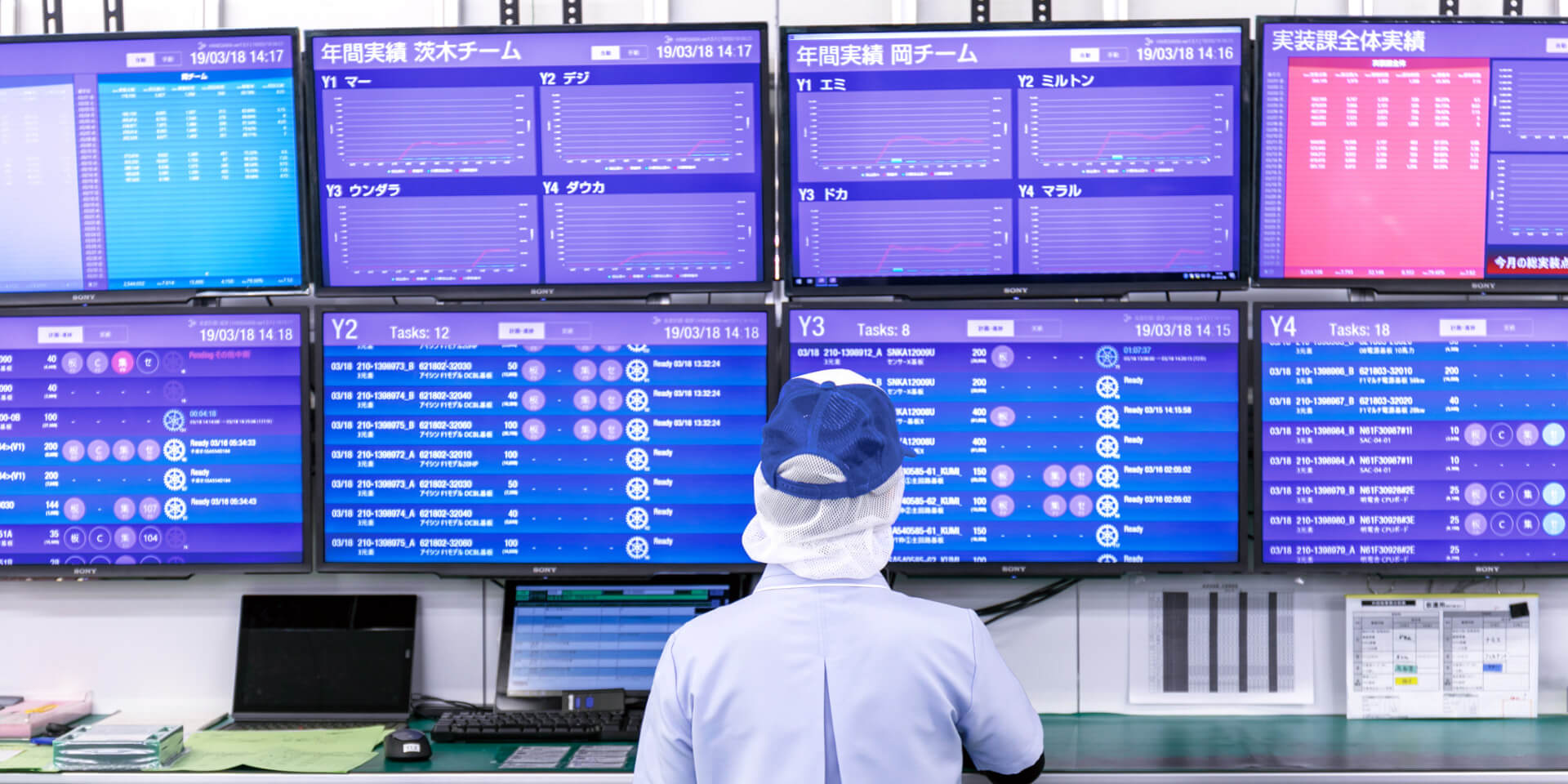
Realization and establishment of smart factory
Realize next-generation production site by visualizing various information such as production progress, production tact time and defects in-process.
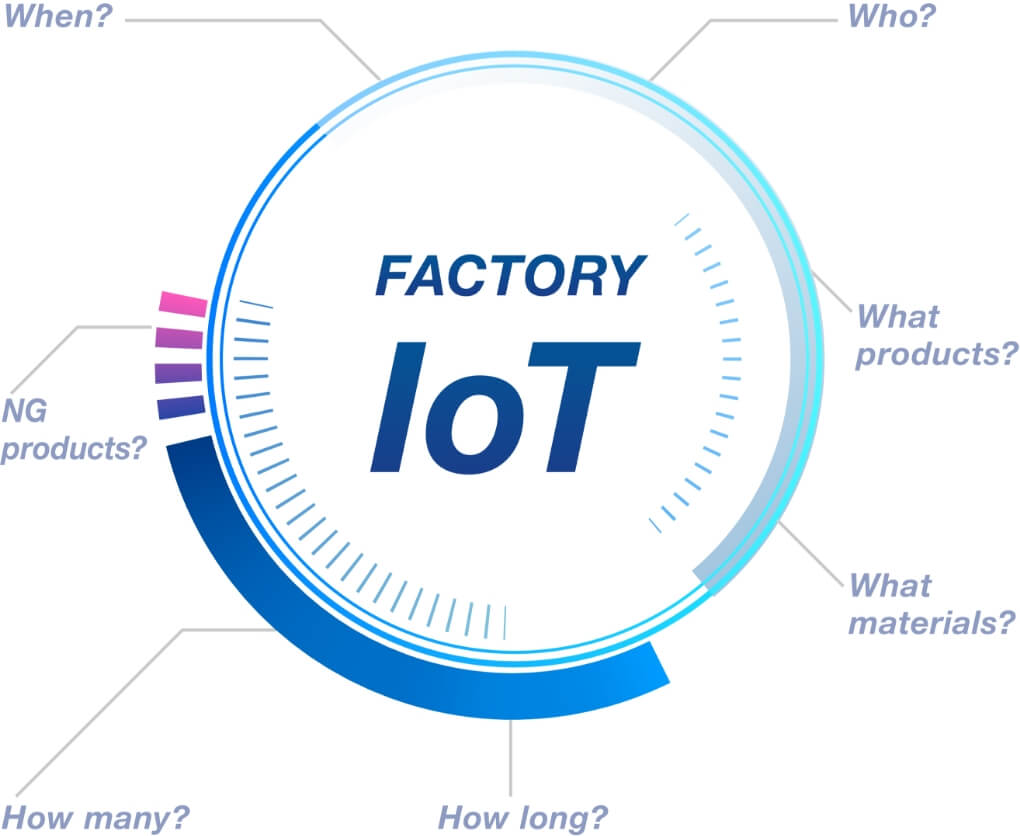