弊社のDX化推進:推進のきっかけとDX推進の具体的な進め方
DX
工場デジタル化
システム開発
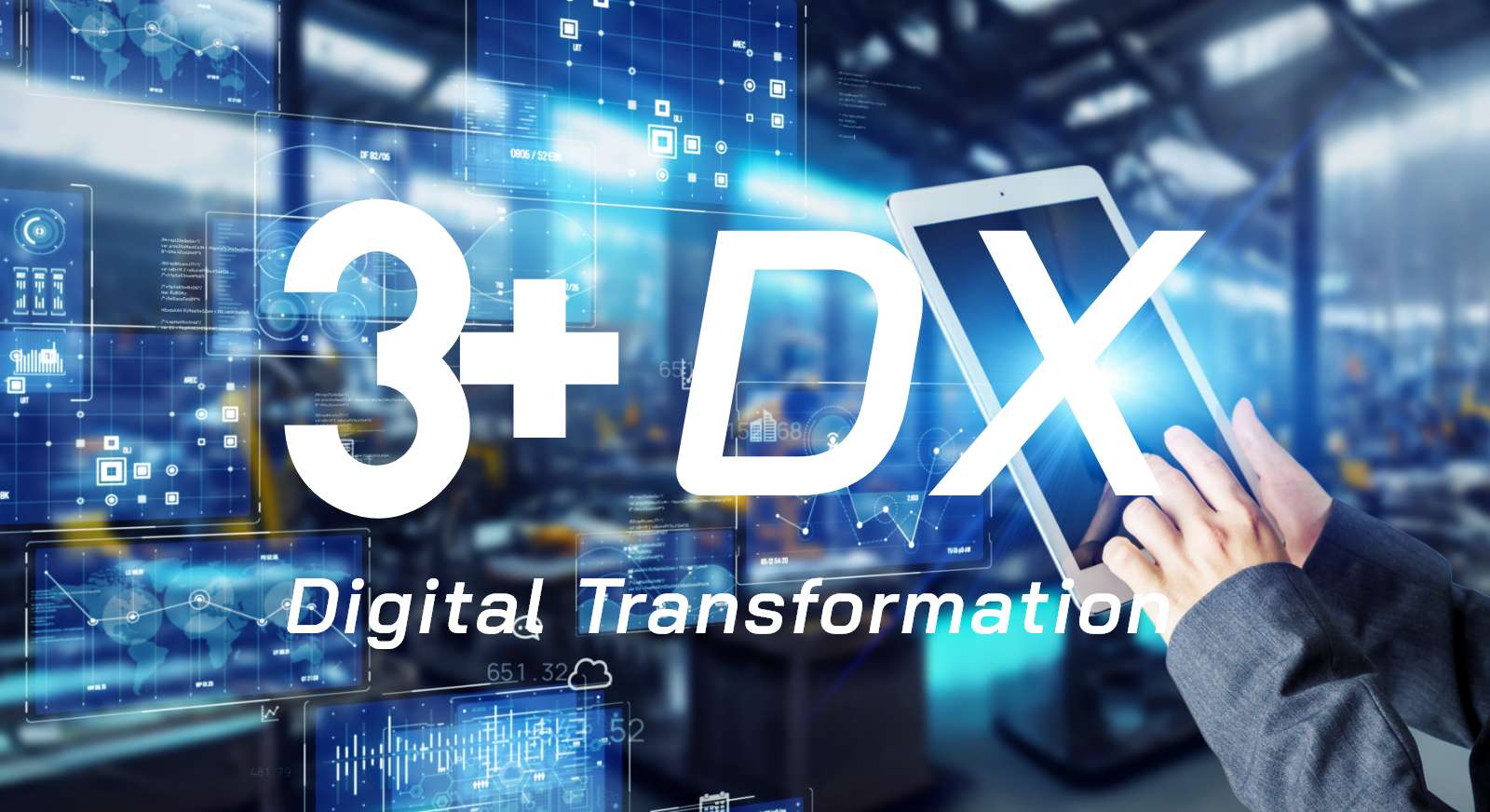
DXを進めることは決めた!けれど…DX推進をどう社員に動機付けさせれば…
こんなことにお悩みではありませんか?
もう少し具体的にお話しすると、DX推進をどう社員に動機付けさせればいいのか、社員がシステム化に向け、抵抗感を持つことなく、社員が一丸となって進めるにはどうしたらいいかなど不安なこともたくさんあると思います。
IT化をなぜ進めてきたか、IT化の目的、進め方、など弊社が実施した方法を例にご紹介させていただき、みなさまのDX推進の動機付けになれば幸いです。
まず最初によく聞かれるのは、IT化のきかっかけをよく聞かれます。それ以外にも下記のようにいくつか聞かれますが、一つずつ説明させていただきます。
IT化導入のきっかけは?
私たちがIT化を導入したのは、ある最終目標を実現するためでした。
そして、その目標を達成するための手段としてIT化を進めてきたのです。
では、その最終目標とは何か?
日々の収益が把握でき、常に原価分析ができる工場の実現
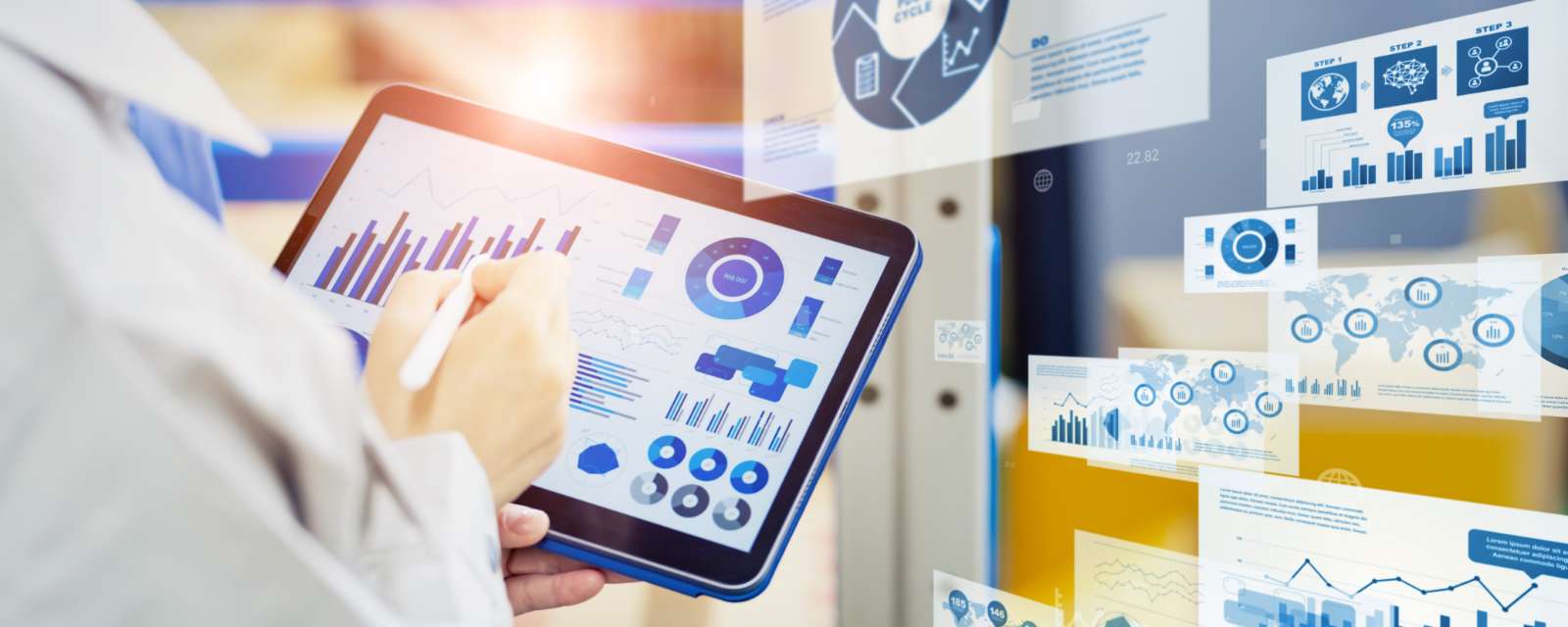
私たちは、日々の収益をリアルタイムで確認し、コストを常に分析できる環境を作りたかったのです。そのための手段として、IT化を進めてきました。
以前、「やってみなはれ、DX」というセミナーでお話ししたことがありますが、これは「なぜ作業日報を作成するのか?」という問いと本質的に同じことなんです。
日々の収益を正しく把握するためには、製造現場で発生するあらゆる生産実績データをリアルタイムで集計できる仕組みが必要です。
しかし、実際には すぐに集計ができないのが現場の現状でした。
生産実績が把握できない問題を、解決するための手段
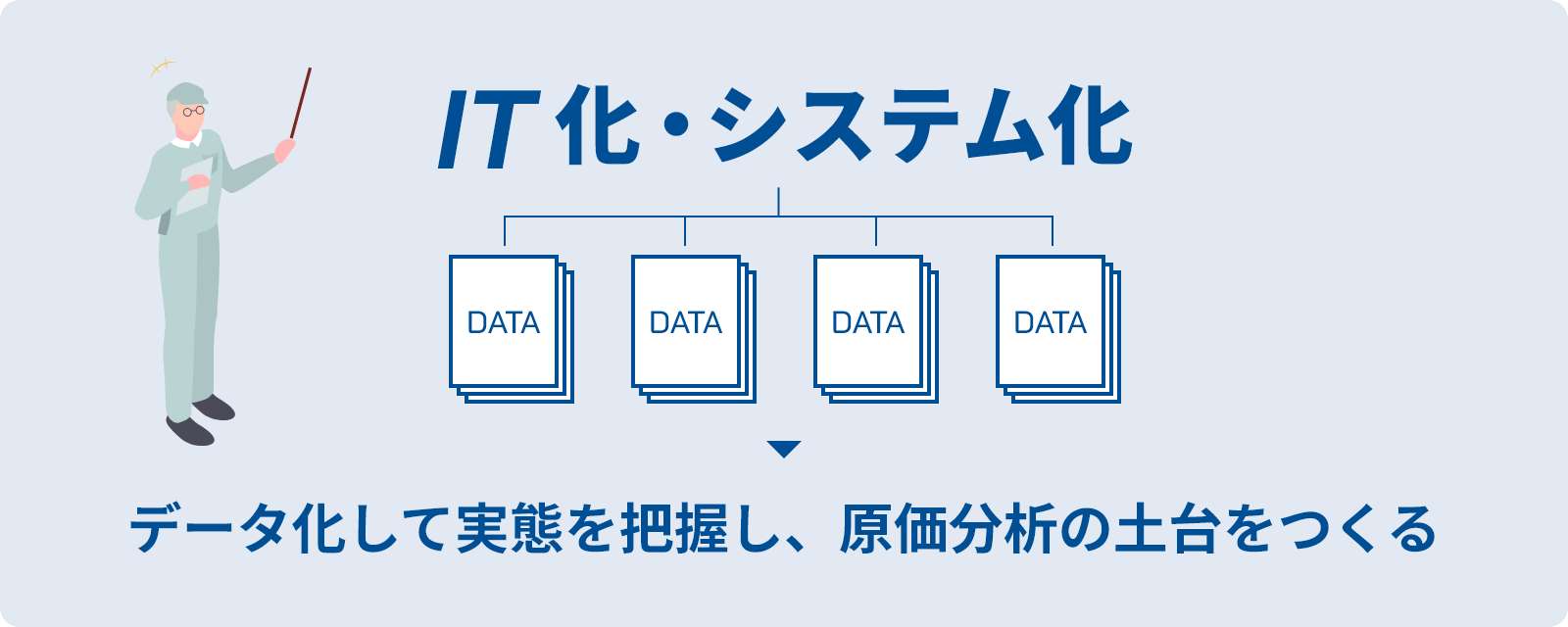
私たちも最初から完璧にデータを活用できていたわけではありません。
生産実績の記録はあるが、集計していない。この場合は集計すればいいのですが、それすらされていなかった。生産実績の記録自体を取っていなかった。最悪なのは、記録を取る環境がそもそもなかった。つまり、簡単に言うと 「生産の実態が分からない状態」 だったのです。この問題を解決するために、システム化を進めることにしました。
実態を正しく把握するためには、まず「見えにくくしている原因」を取り除く必要があります。
もう少し具体的に言うと、
・製造の管理者に『この製品はいくつできるの?』と聞くと「おおよそ100個くらいですね」
・『この製品の工程内不良は?』と聞くと「だいたい10個ぐらいでしょうか」
こんな感じで、 「正確な数値ではなく、感覚的な答え」が返ってくることってありませんか?
こうした 「なんとなく」 で進んでいる状態では、正しい分析も改善もできません。
だからこそ、私たちは IT化でデータを可視化し、生産現場の実態を正しく把握することを目的にしました。
私たちのIT化の目的は、単にシステムを導入することではありません。
「データという事実を把握することで、生産現場の実態を明らかにすること」こそが本来の目的です。実態が明確になれば、次に進むべき改善点も見えてきます。
明確になれば、次に進むべき改善点も見えてきます。
よく言われる例ですが、
・製造課長は知らないが、主任は知っている
・主任は知らないが、リーダーは知っている
・最悪の場合、リーダーは知らないが、作業者は知っている
こういった 「情報のズレ」 が製造現場ではよく発生します。
現場の本当の状況を知らずに意思決定をしてしまうと、的外れな改善策を打ってしまうことになります。そのため、 「知らなかった事実」を把握する手段 としてIT化を進めてきました。
IT化だけでは問題は解決しない
ただし、IT化を導入したからといって、それだけで全ての問題が解決するわけではありません。大切なのは、事実を把握することで、問題を明確にし、その問題を一つずつ潰していくことです。 IT化は単なるツールではなく、 「改善のテーマを見つけ出すための手段」なのです。
IT化によって明らかになった問題を改善していくことで、初めて投資効果が生まれます。
私たちがIT化を進めたきっかけは、「実態が見えにくい製造現場を、データで見えるようにし、原価分析ができる環境を構築すること」にありました。
その結果として、正確な収益管理ができるようになり、より精度の高い経営判断が可能になるのです。
具体的にどのように進めてきたか?
次によく聞かれるのは、「具体的にどのようにIT化を進めてきたのか?」という質問です。
私たちは、システム化を進めるにあたり、「社内で3つのルールを絶対に守る」と決めました。
この3つのルールをクリアしない限り、システムの仕様を見直さなければならず、開発のGOサインを出すことはできません。
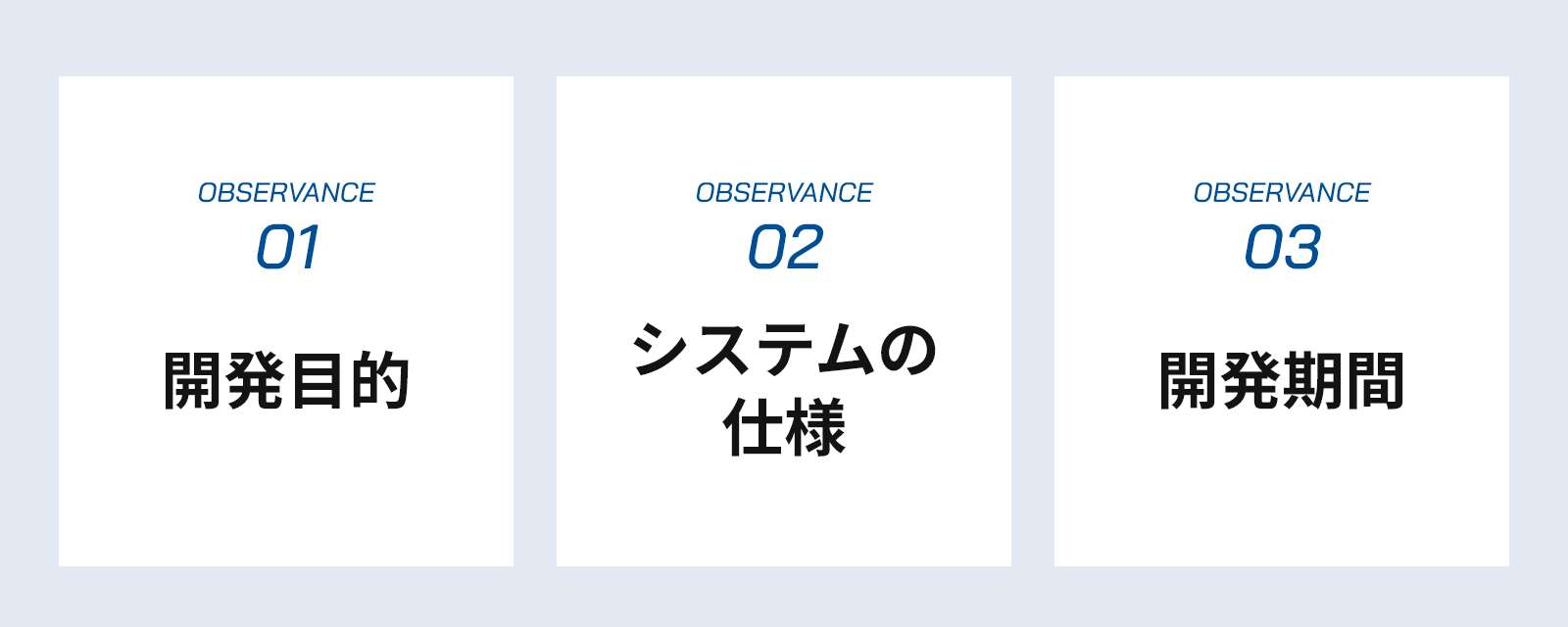
開発目的は「あれもこれも」はNG!
開発を進めるにあたり、「あれもやりたい」「これも欲しい」と要望が増えがちですが、
私たちは 「目的をひとつに絞る」ことを徹底しました。
目的がブレると、システムが複雑になり、開発期間が長くなるだけでなく、結果的に現場に適さないものになってしまいます。
「システムは 小さく作り、スピーディーに回す」ことが重要です。
システムの仕様は現場の責任者が決める
システムを導入するとき、どのような業務フローにするのか、どのデータを活用するのか、
「現場の管理監督者が仕様を決める」ことを原則にしています。
開発をエンジニア任せにすると、使いづらいシステムができあがってしまうことがあるため、現場の責任者がしっかりと方向性を定めることが大切です。
システムの開発期間は3ヶ月
仕様作成を1ヶ月、開発を2ヶ月、合計3ヶ月以内で稼働させることを原則としています。
この期間を超えると、仕様変更やニーズの変化に対応しづらくなり、結果的に非効率になるため、「短期間で結果を出し、次の改善へと進めるサイクルを回す」ことが重要だと考えています。
どのように人材育成してきたか?
次によく聞かれるのが、「システムを構築できる人材をどうやって育成してきたのか?」という質問です。
私たちは、以下の3つの力を育成することが重要だと考えています。
システム導入後の姿を描く力 (システム開発は外部で実施)
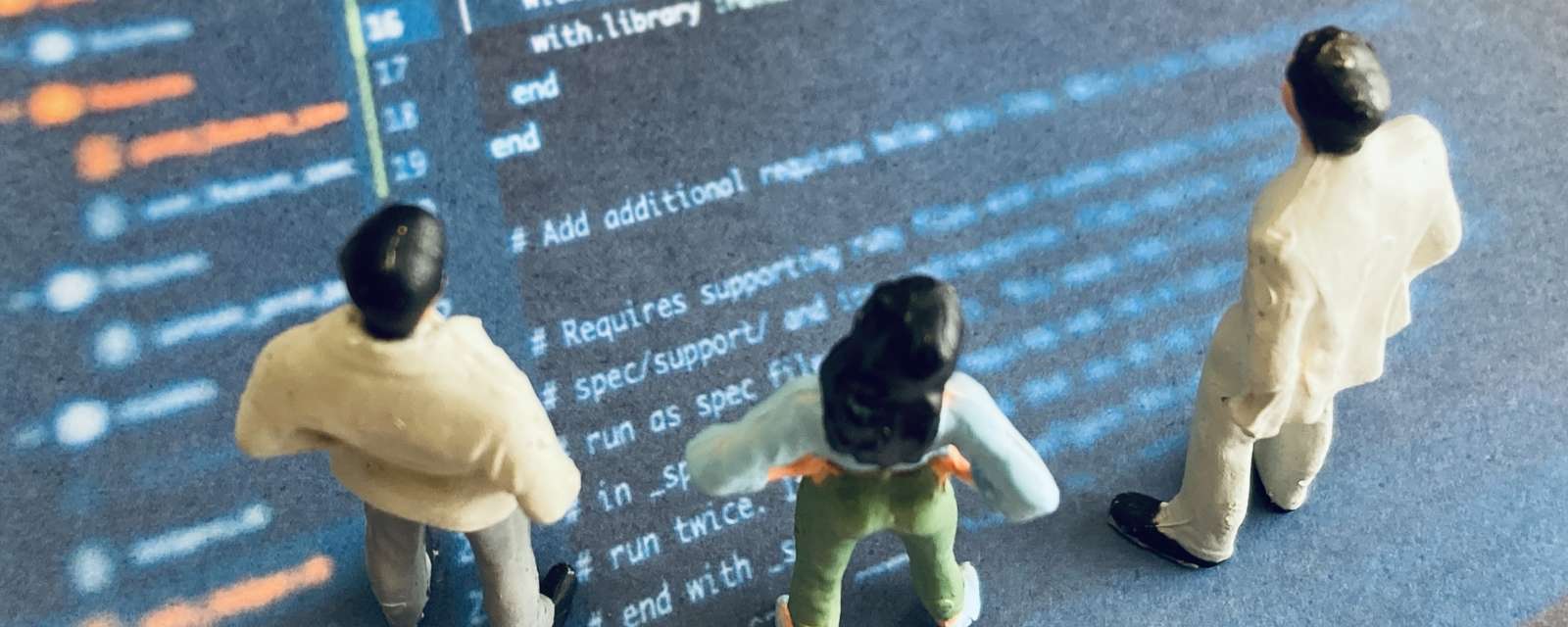
弊社で稼働している各種のシステムは、すべて外部のシステム会社で開発しました。 正直なところ、私たちはシステム技術には詳しくありませんし、それが必要だとも思っていません。システム開発は、専門のエンジニアがプログラム設計をすればいいと考えています。 重要なのは 「どんなデジタル技術を使うか」ではなく、「どんな仕組みを構築したいのか」 です。
例えば、
・どんなデータが必要なのか?
・どんな業務フローにするのか?
・システム導入後の製造現場の姿はどうなるのか?
これらを具体的に描く力が求められます。
また、問題点を1つに絞り小さくシステムを作ることで、仕様を明確にし、自分たちのやりたいことがブレずに実現しやすくなります。
精度の高いシステム仕様を構築する力
私たちは 「リリース後、即稼働」を目標にしています。 システム導入後に「ここが違う」「こんなはずじゃなかった」とならないように、仕様検討の段階で徹底的に精度を高めることを重視しています。
仕様がしっかり固まっていれば、
・現場での受け入れがスムーズになり、
・リリース後すぐに活用されるシステムになります。
逆に、精度の低い仕様で開発してしまうと、リリース後に現場で使われず、結局「失敗プロジェクト」になってしまいます。
精度の高いシステムを作ることで、現場での市民権を得て、スムーズな定着につながるのです。
情報を結ぶ力
次に求められるのが「情報を結びつける力」です。
製造現場では「ほしいものを、ほしい時に、ほしい量だけ、ほしい場所に供給する」ことが求められます。
「ほしいもの」って何?「ほしい時」っていつ?「ほしい数」っていくつ?「ほしい場所」ってどこ?を具体的に考えてみましょう。
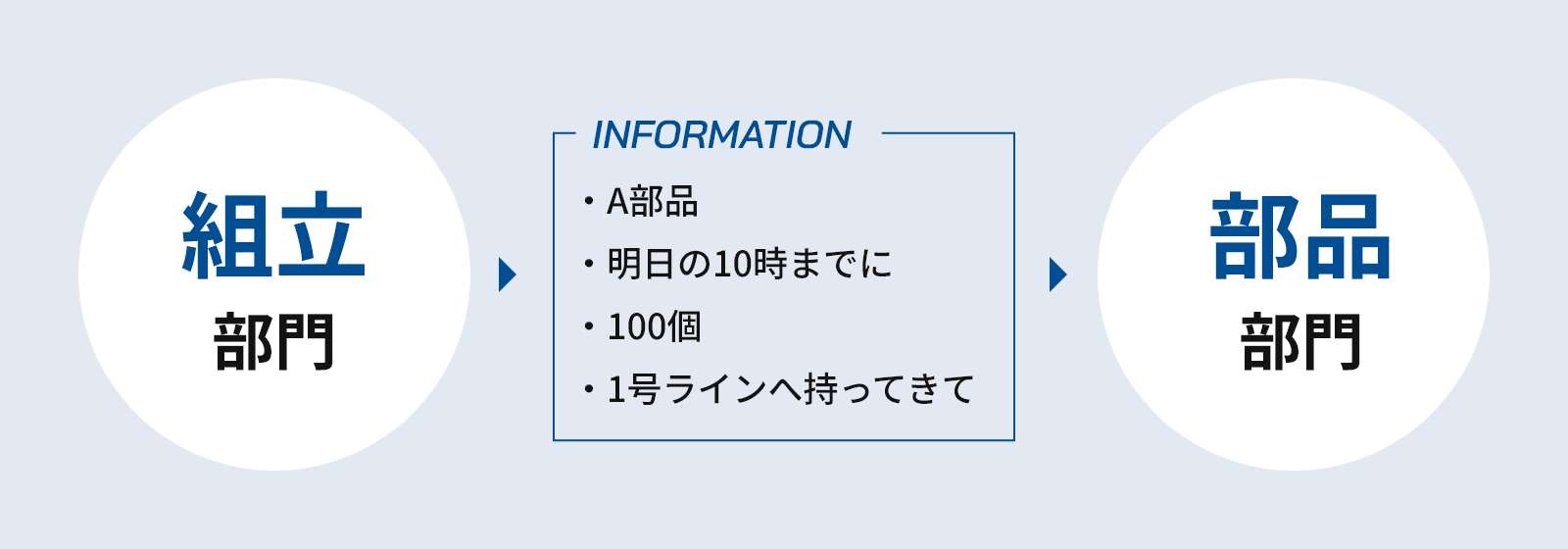
例えば、
組立工程が、部品を払出している部品部門に対して、「A部品を、明日の10時までに100個、1号ラインに持ってきて」と伝える。
これも、情報の流れの一つです。
こうした「正確で明確な情報を伝えること」で、組立部門と部品部門がスムーズに連携できます。これこそが IT化の本質であり、どの情報を、どの部署と、どう結びつけるかを考える力が求められるのです。
このようなスキルを、現場の責任者が実践を通じて身につけていくことが重要です。
システムエンジニアが社内にいないからDX推進が進まない、という声をよく聞きます。しかし、システムエンジニアがいなくてもDXは推進できます。
求められるのは「プログラム設計のスキル」ではなく、「DXをどう描くかの力」です。
そのため、弊社では「DXを推進するための考え方やスキルを育成すること」を重点的に進めています。
導入時の抵抗はなかったか?
4つ目によく聞かれるのが、「導入に対する抵抗はなかったか?」という質問です。
現場の中心人物を味方にする
たしかに、DXを進めることは企業の文化を変えることにつながります。 変革には必ず抵抗があるものですが、それをどう乗り越えるかが重要です。
そのために私たちが意識したのは、職場の中心人物を味方につけることです。 どの現場にも「もさ」と呼ばれる影響力のあるキーパーソンがいるものです。
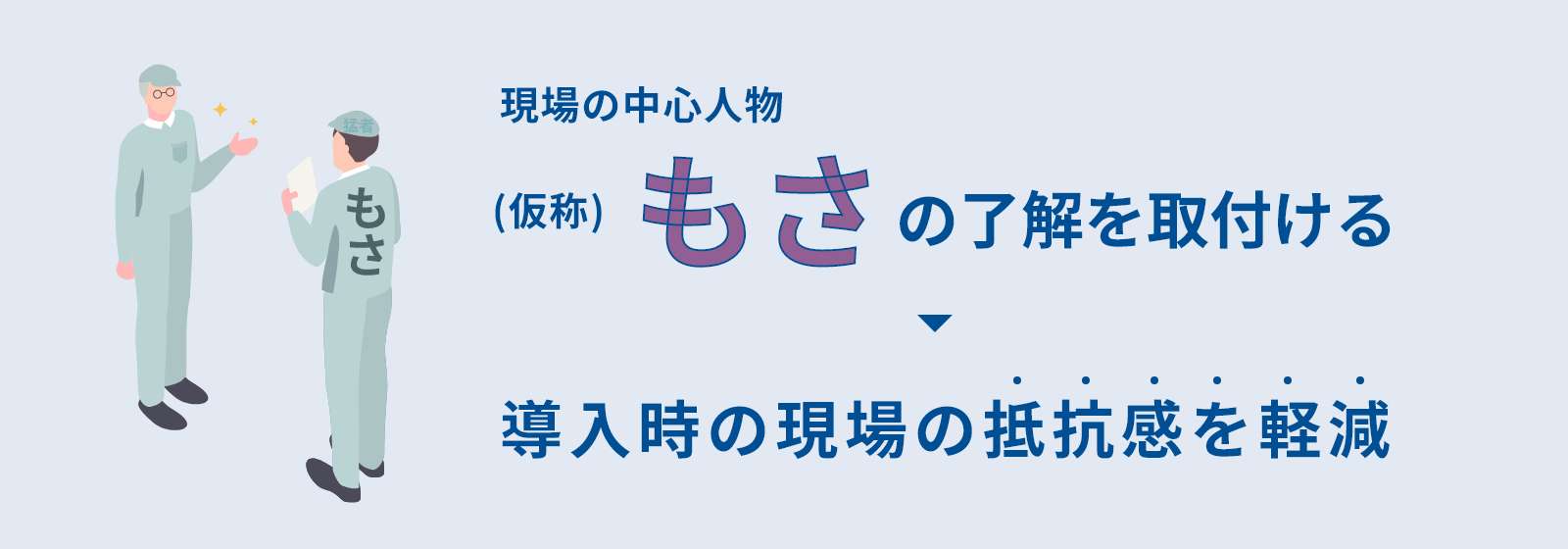
この「もさ」の方に、導入の目的やシステムの仕様、画面の操作性などを事前に説明し、納得してもらうことを徹底しました。
「これなら使ってやる」
この一言がもらえるかどうかがポイントです。 現場の責任者が仕様を決め、「もさ」の了解を得る。
「もさ」を味方につけることで、現場の抵抗感をなくし、スムーズな導入につなげました。
使ってもらうのではなく、使いたくなるシステム
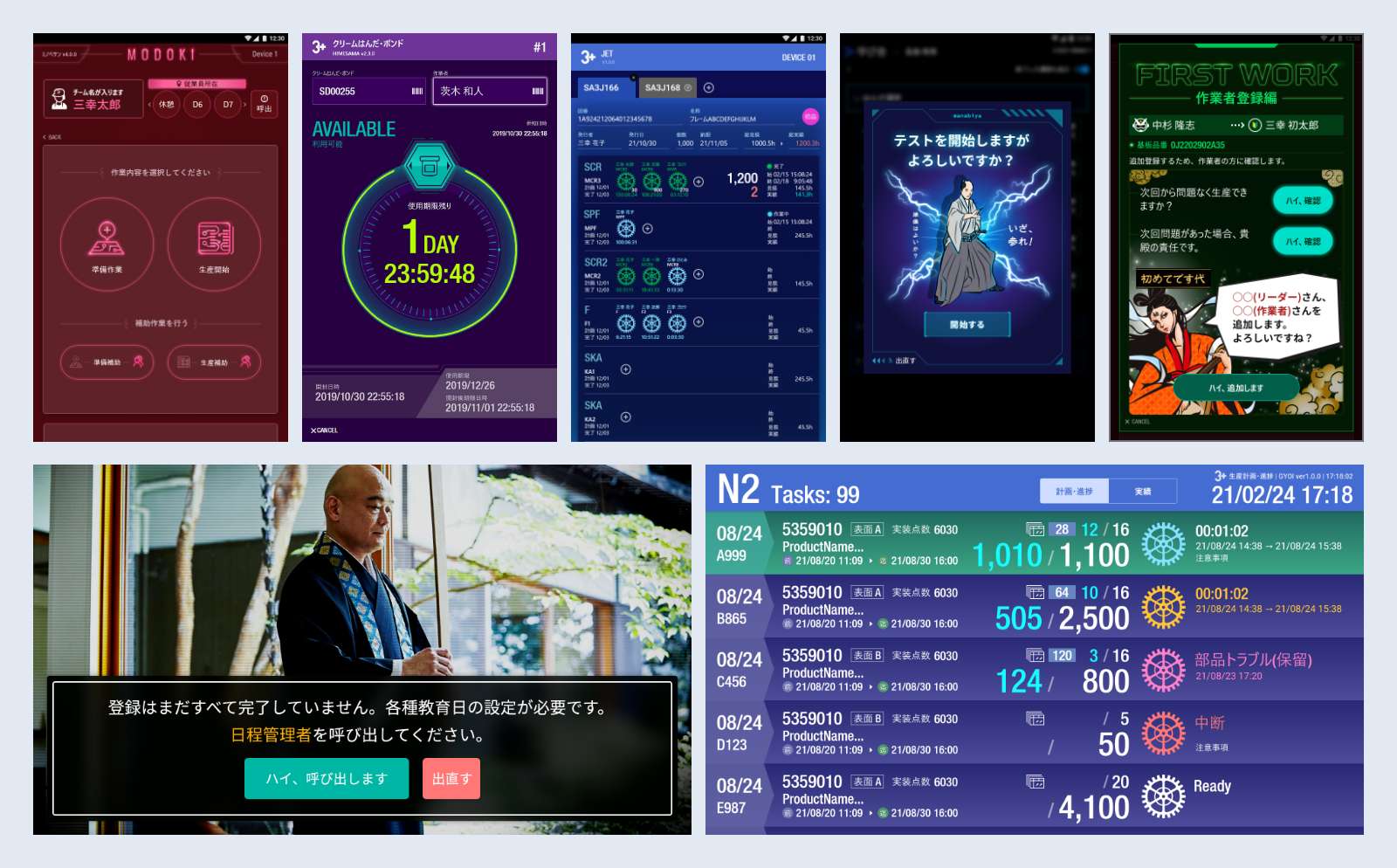
システムエンジニアは機能や動作の正確性を重視しがちですが、 ユーザーが「使いやすい」「見やすい」と感じるかどうかには意識が向かないこともあります。
そのため、タブレットの操作画面やモニターの表示デザインはデザイナーに依頼しました。
システムは「使ってもらうもの」ではなく、「使いたくなるもの」であるべきです。 操作性だけでなく、画面レイアウトや配色にもこだわり、作業者が直感的に使いやすいデザインにすることを重視しました。
インフラの充実
意外に見落とされがちですが、インフラの整備も導入成功のカギです。
私たちは応答速度を1.5秒以下にすることを目標にしました。
なぜなら、人間は2秒以上の待ち時間にストレスを感じると言われているからです。
「ちょっと遅いな…」と思うだけで、使われなくなるリスクがあります。
そのため、システム導入前からインフラ整備をしっかり準備することを徹底しました。
今後の課題は?
最後になりますが、その他によく聞かれるのが、「今後の課題は何か?」という質問です。
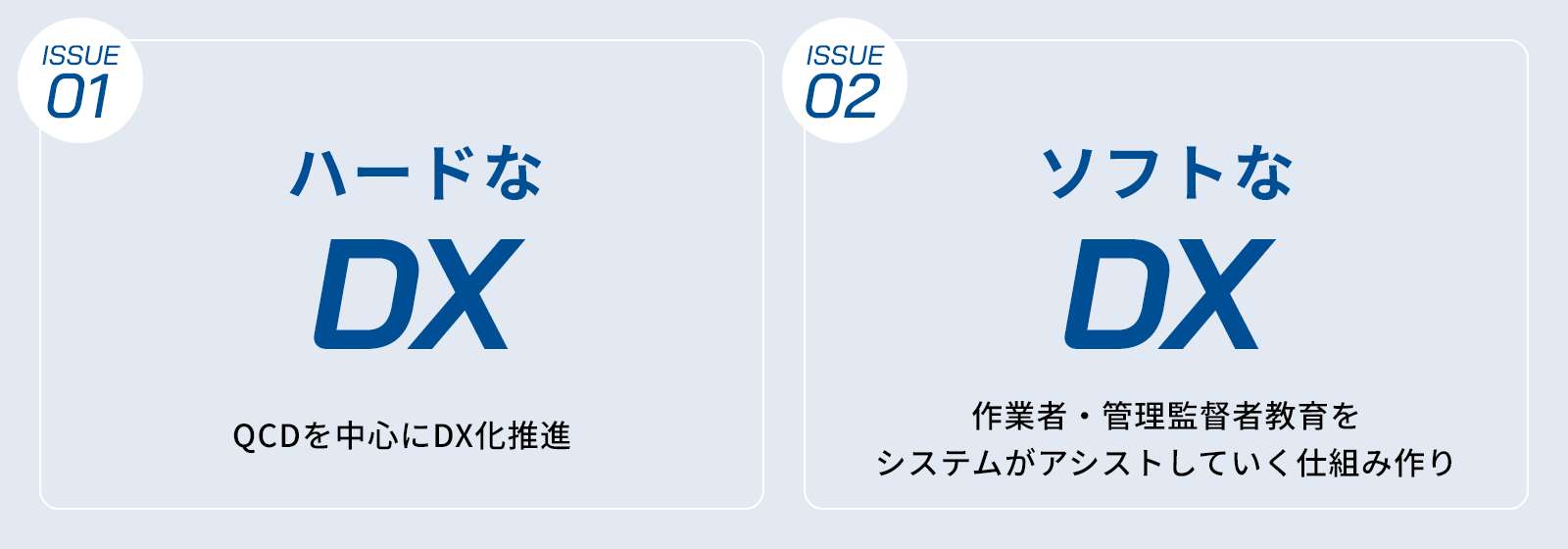
ハードなDX推進
私たちは「ハードなDX」という言葉を使っています。
これは、製造現場の品質向上、生産性向上、QCD(品質・コスト・納期)の最適化を目的に、DXを進めることを指します。弊社の製造現場における最大の使命は、いかに直接加工費を下げるかです。そのために、DX化で得たデータを分析し、問題点を見つけ出し、改善を実施することでコストダウンを実現する。
これを、これからも継続していきます。
ソフトなDX推進
一方で、私たちは「ソフトなDX」も進めています。
これは、作業者や管理監督者の教育を、システムがアシストする仕組みを作るという取り組みです。現在進行形で取り組んでいるのは、教育訓練の計画立案と実施管理のシステム化です。
例えば、
・教育訓練計画を立てたものの、実施されていない
・作業者の個人のスキル評価ができていない
こうした課題がよくあります。
「教育は実施されたの?」と聞くと、「忙しくて忘れていました」という返答が返ってくることも少なくありません。
このような「計画と実施のズレ」を防ぐために、 システムで教育計画の立案から実施までを管理し、管理監督者をアシストする仕組みを構築しています。
高機能なシステムを作っても、運営するのは現場の管理監督者です。
管理監督者の力こそが現場の改善力であり、その改善力を高めることが企業価値の向上につながると考えています。
そのため、今後はソフトなDXを推進し、管理監督者の人材育成により力を入れていきたいと考えています。
Written by
2016年より新たな企業方針を掲げ、ITツールを活用した製造現場のデジタル化を進めてきました。弊社が培ってきたノウハウを少しでもお役立ていただければ嬉しいです。
CONTACT US
3+サンプラスのお問合せについて
『3+サンプラスの件』とお伝えいただけましたら担当者へおつなぎいたします。
まずはお気軽にお問合せください。