導入したシステム
案件別工程間
進度管理システム『JET』
株式会社松原製作所 生産管理部 主任 M 様 [業種:金属加工]
製品を探す時間が無くなり、画面を通して作業者の方と話が出来るため指示がしやすくなりました。ペーパーレス化も大幅促進。
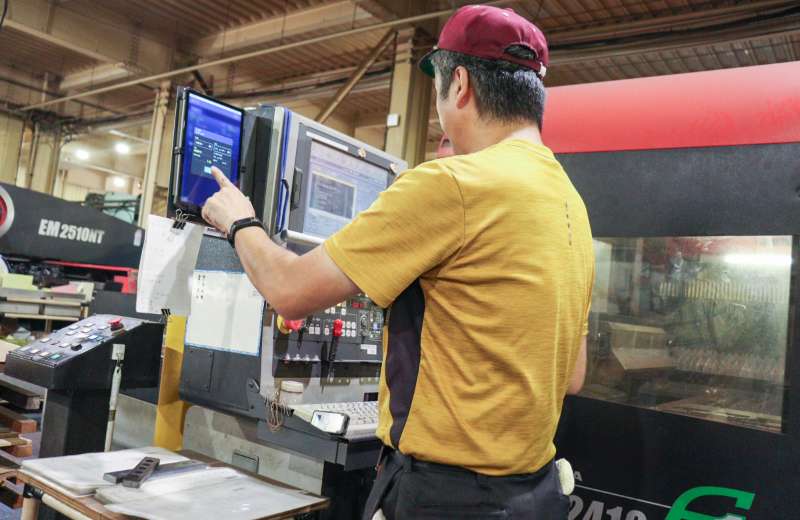
QUESTION01
普段はどんな業務をされているかを教えてください。
生産管理部で主任を務め、基本的な業務としては受注管理と人事管理を行っております。生産管理部門ですので基本的には製品の生産指示業務を行っています。
QUESTION02
サンプラスを導入される前に困っていた事、課題を教えてください。
製品がどこにあるかが分からなかったのが一番の問題点でした。
現在はサンプラスを導入した事で、製品がピンポイントでどの工程にあるか分かるので現場に見に行くことも少なくなり、確認も容易になりました。
また、以前は紙の日報だったので生産数を書いてくれない人がいて、いくつ生産したのかが把握できませんでしたが、今はサンプラスで生産数の入力は必須になっているのでしっかり把握できています。その2つが大きな悩みでした。
QUESTION03
他にもいろいろシステムがある中で、サンプラスを選んでいただけた理由を教えてください。
上司が工場見学でお邪魔させていただいたのですが、「サンプラス良かったよ」と提案され、私も実際に工場にお邪魔して見学させていただいた時に画面表示の見た目が良く、パッと見て分かる感じがこのシステム使えそうだなと感じました。
QUESTION04
サンプラスを導入され、使用されている中での使用感、操作感等はいかがでしょうか。
使用感はとても分かりやすく、色々打合せした中で弊社に合わせた方向に持っていっていただいたと思っています。
現場の方もスムーズに使えていると言っています。
管理する立場として私も操作しやすいです。現場の管理とかけ離れたシステムだと使えないと思うので、カスタマイズしていただいて良かったです。
最初はタブレットを使う事への基本的な抵抗はありましたが、教育した事で現在は問題なく使用出来ていますし、これは使えないですという人はいませんでした。
QUESTION05
サンプラスを導入されて主にどんな所に効果があったか、変化があったか教えてください。
製品を探す時間が無くなり、画面(見えまっせ)を通して作業者の方と話が出来るから指示がしやすくなりました。
以前は製品をスタート工程から順に探していたので30~40分程かかっていましたが、半分ぐらいの時間で探せるようになりました。
また、生産指示の方法も今までは紙で出していたので、紙が無くなってしまいきちんと作業が出来ていないという事がありましたが現在はタブレットで生産指示を出しているのでそういった問題もなくなっています。
紙の枚数としては月に4000枚程出していましたが1800枚程(2200枚減)になりました。
紙を買うペースも減りましたし、コピー機を占領する事が少なくなりインク使用量も少なくなりました。
QUESTION06
今後、導入システムの拡張やシステムの追加導入等、
検討されている場合はどのような事を考えられているか教えてください。
現在は図面を紙で用意しているので、タブレットで図面が見れる機能を追加したいと思っています。
CONTACT US
3+サンプラスのお問合せについて
『3+サンプラスの件』とお伝えいただけましたら担当者へおつなぎいたします。
まずはお気軽にお問合せください。